I spent the whole day up in Oswego. The location was fabulous, a crazily canted old stone building right at the mouth of the Oswego River opening onto Lake Ontario with tugs, barges, and cranes all busying about. But my sightseeing only came in glimpses as I lugged dirty insulated panels out to the truck. I was tearing out a walk-in cooler and freezer. I was able to get it all disconnected, knocked down, and loaded in one long slog, but it warn’t easy. Some of the panels were in bad shape, but I should have enough to make a single freezer, 11 feet wide and between 6 and 12 feet deep depending on how I eventually configure it. My initial thought is that I’m going to use the freezer panels as a framework and install an additional 2″ foam layer inside, but I need some time to work out those construction details.
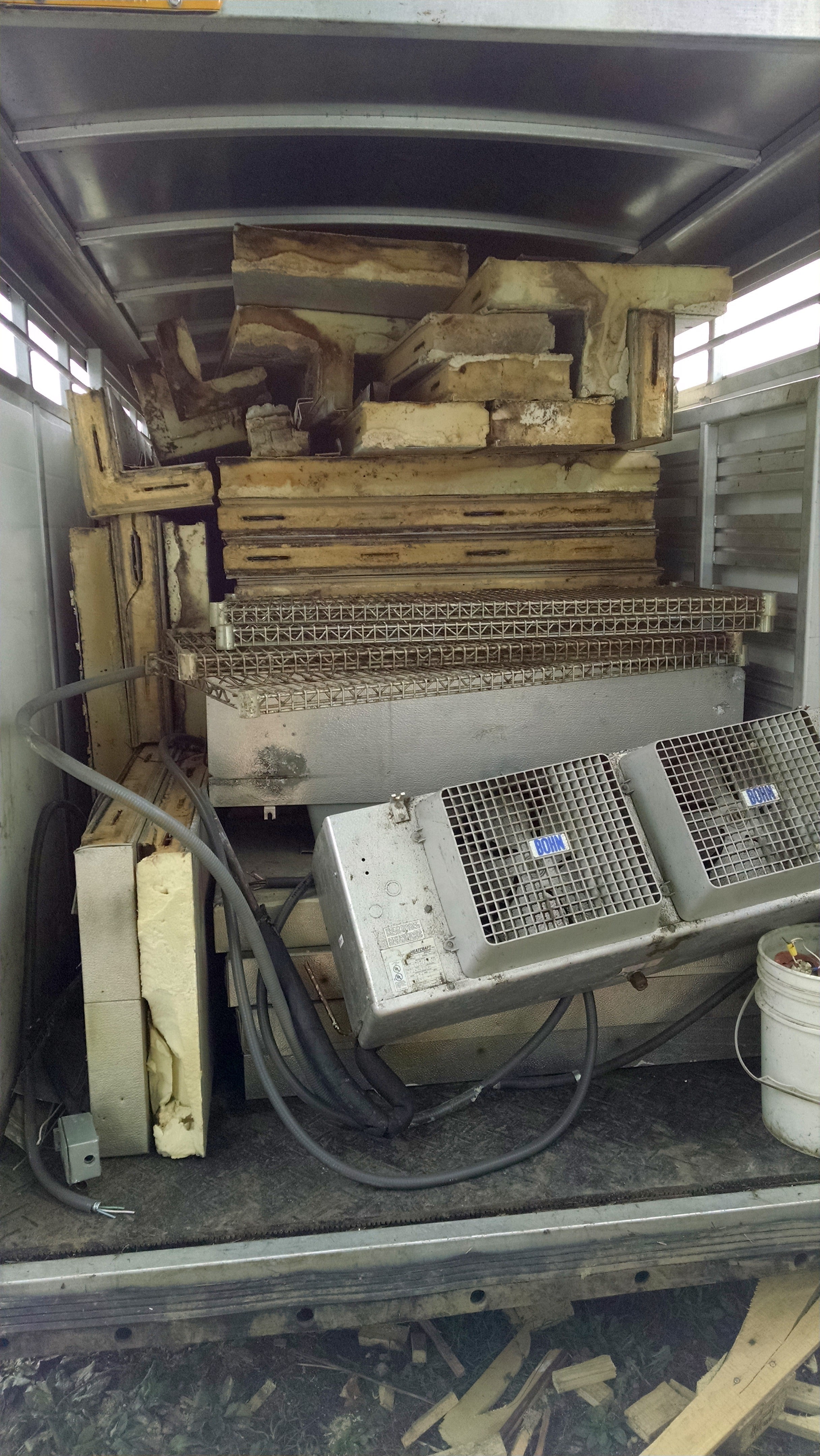
This latest acquisition will eventually go in the shed behind our house. We currently use ten freezers (not counting the little one above the fridge in the kitchen). As we have increased our sales we’ve found that we never have enough freezer space. Chest freezers are more efficient, but they take up a lot of floor space. Upright freezers theoretically allow us to store more per square foot, but their shelving configurations invariably are incompatible with whatever boxes we are trying to stow. In either case, we are out of room to add new freezers. The ideal solution would be to rent cold storage space, but the nearest cold storage requires a two-hour round trip, making it an inconvenient solution. All those considerations make the walk-in the only feasible option for our situation.
I won’t be able to start working on the walk-in freezer until this winter, so for the time being I’ll continue to use the humming herd of freezers. Whatever doesn’t fit I’ll truck out to the commercial freezer warehouse in Utica. For all the time Rachel and I spend shuffling boxes between freezers, we are really looking forward to having a more workable frozen storage facility right here on the farm.
3 thoughts on “A Bigger Freezer”
Oh man, what a score! As you know I’ve been looking for freezer capacity for a while. The one really useful design detail to walk-ins I was not aware of until digging into the topic is the floor venting. I talked with a commercial refridge guy and he said venting under the floor was absolutely critical, even if you insulate the living daylights out of it. He’d seen DIY walk-ins that had heaved and cracked their concrete slabs terribly when people disregard this rule. He said his go-to method was to design the compressor fans so they pushed the warm air under the unit on its way out.
I’m of mixed minds whether it was a score. As I disassembled it, I discovered that some of the panels and hardware were in bad shape, so the value of the deal steadily declined as I found more problems. Probably fatigue played a factor in diminishing my satisfaction with the purchase as the day wore on. Now I look out at the pile of parts and see another looming project. But I’m sure that after I leave it alone for a month or two I’ll be eager to get back into it.
Thanks for the tip about the slab venting. In this case I’ll avoid that since the floor in the shed already has a crawlspace underneath. Interestingly, neither the cooler nor the freezer section had any insulation. I guess that in a cold climate (and especially back in 1989 when this cooler was built) the payback period for insulating a cooler floor was long enough to justify skipping it, but it doesn’t make any sense to omit insulation on a freezer floor.