I never expected finding a reliable, effective feeder for our pasture raised chickens would be such a challenge. Over the past twelve years I have built countless feeders. And I’ve tried at least ten different commercial feeders trying to find something that really worked.
Along the way I came up with a pretty good homemade design for laying hens, but for broiler chickens I keep coming back to the Kuhl 50 lb hanging feeder as the best option. I like that it has a feed tray with a large lip, preventing the chickens from scraping the feed out with their beaks and wasting it on the ground. The solid tray dividers prevent side-to-side swipes that can also lead to spilled feed. Plus, the round design means that the chickens can access the feeders from all directions.
Providing feed to pasture raised chickens is always a challenge, and feeders need to be tough. In any situations chickens are constantly bumping the feeders, but in a pasture environment there are additional shock loads. We move our chickens to fresh grass, so the chicken shelters travel thousands of feet each season. All that movement is great for the grass and for the chickens, but it puts strain on the components of hanging feeders.
We discovered that the Kuhl hanging feeders have a fatal design flaw. They might work perfectly fine in barns, but with all our pasture rotations, they always break. The problem is that they are held together by a steel bolt threaded into a light aluminum shaft. Eventually that bolt strips out and the feed tray falls out the bottom. I have tried all sorts of things to fix it, including using both blue and red formulations of Loctite and even epoxy. None of these are durable solutions. I’ve also tried drilling out and re-tapping the aluminum, but that only buys a little time. The aluminum is just too brittle, and I have a feeling that the corrosion between dissimilar metals, especially in a wet, grassy environment may be hastening its demise.
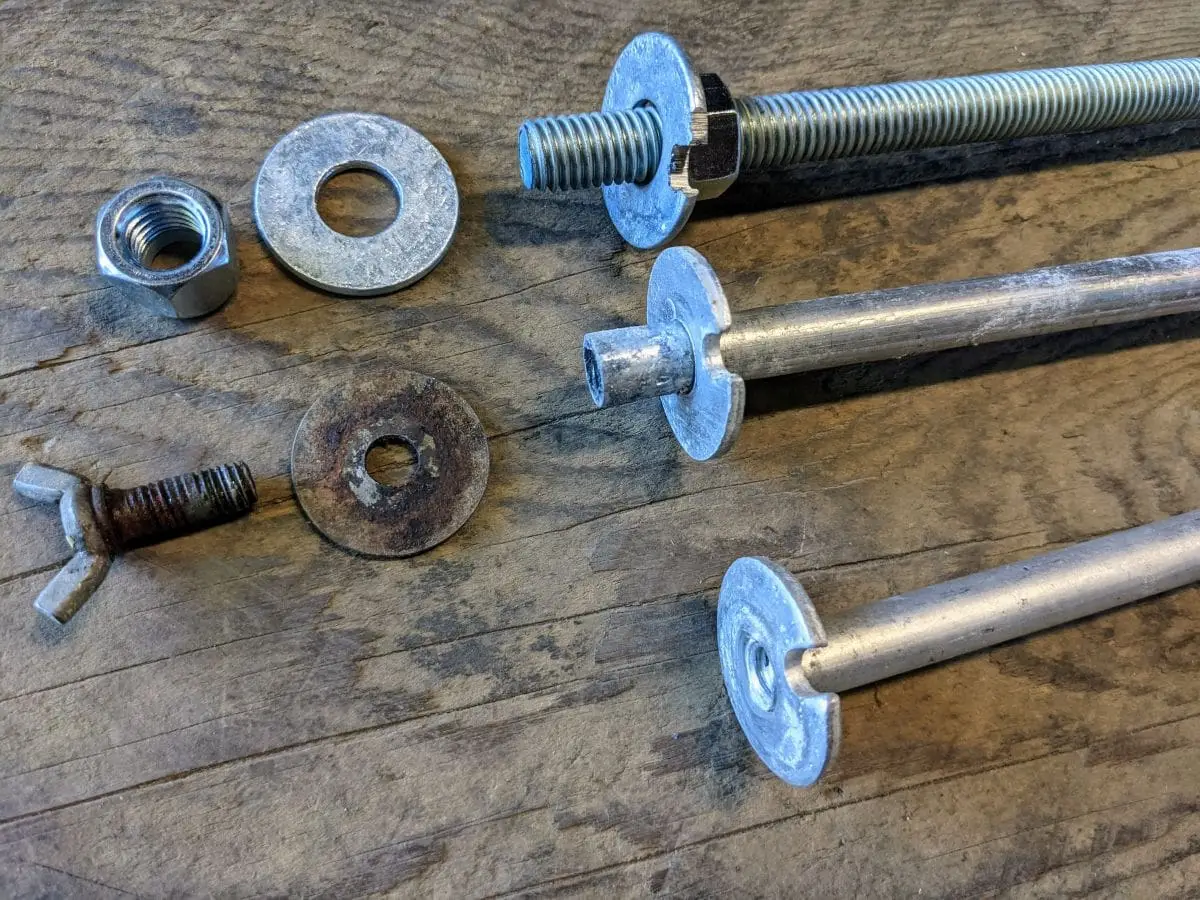
Rather than giving up on the feeders, I decided to repair them. But this time I’m going with all steel construction. No more aluminum. I am cutting 1/2″ steel threaded rod into 19.5″ pieces and welding on a lock washer at one end as a hanger. The other end just gets the threads cleaned up so I can thread nuts back on.
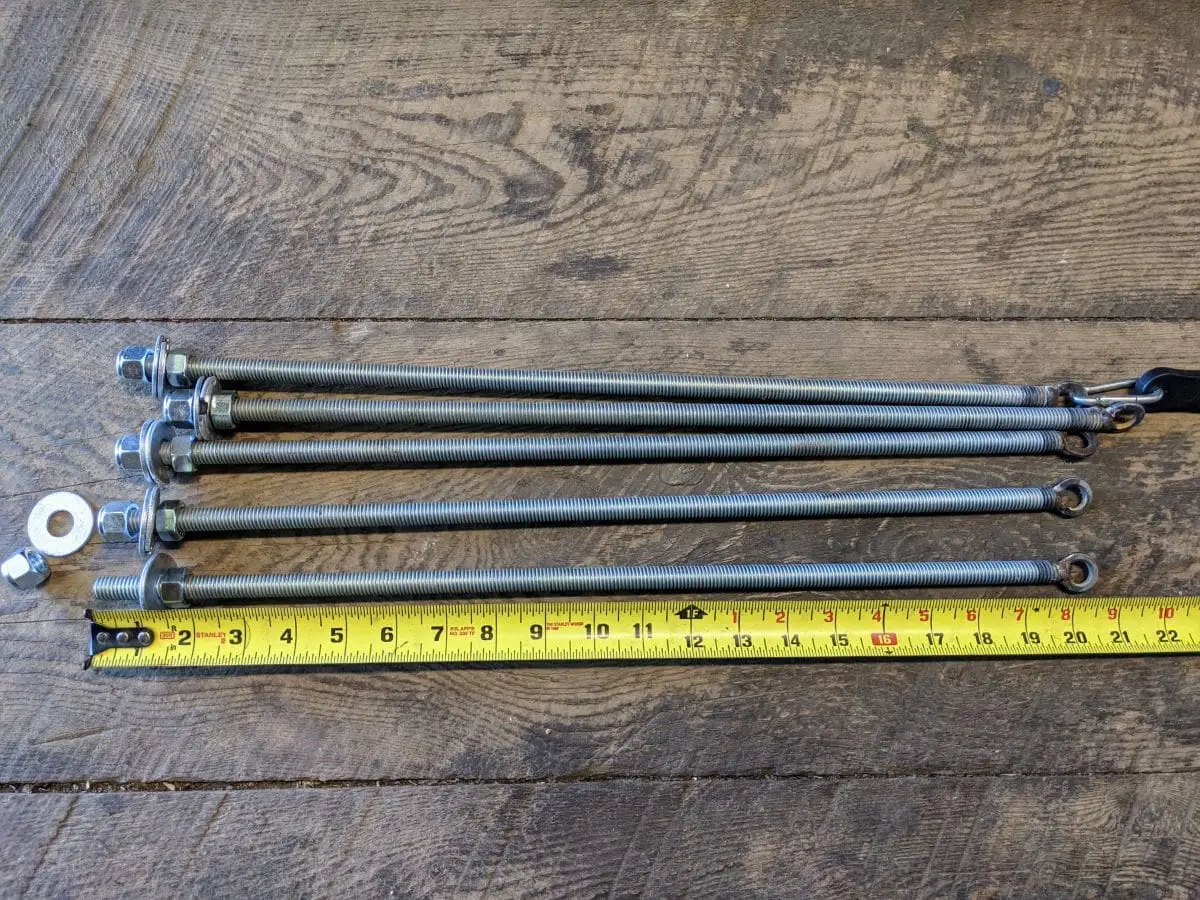
The inside of the feeder has a small raised bump and the original aluminum rod’s washer is notched around that bump. I just use an angle grinder to make similar notches in 1/2″ washers. Note in the picture below that I’m using a regular 1/2″ nut next to the notched washer, and then a nylon lock nut on the bottom. I have also applied blue Loctite on the non-locking nut, but I’m not sure if this is necessary.
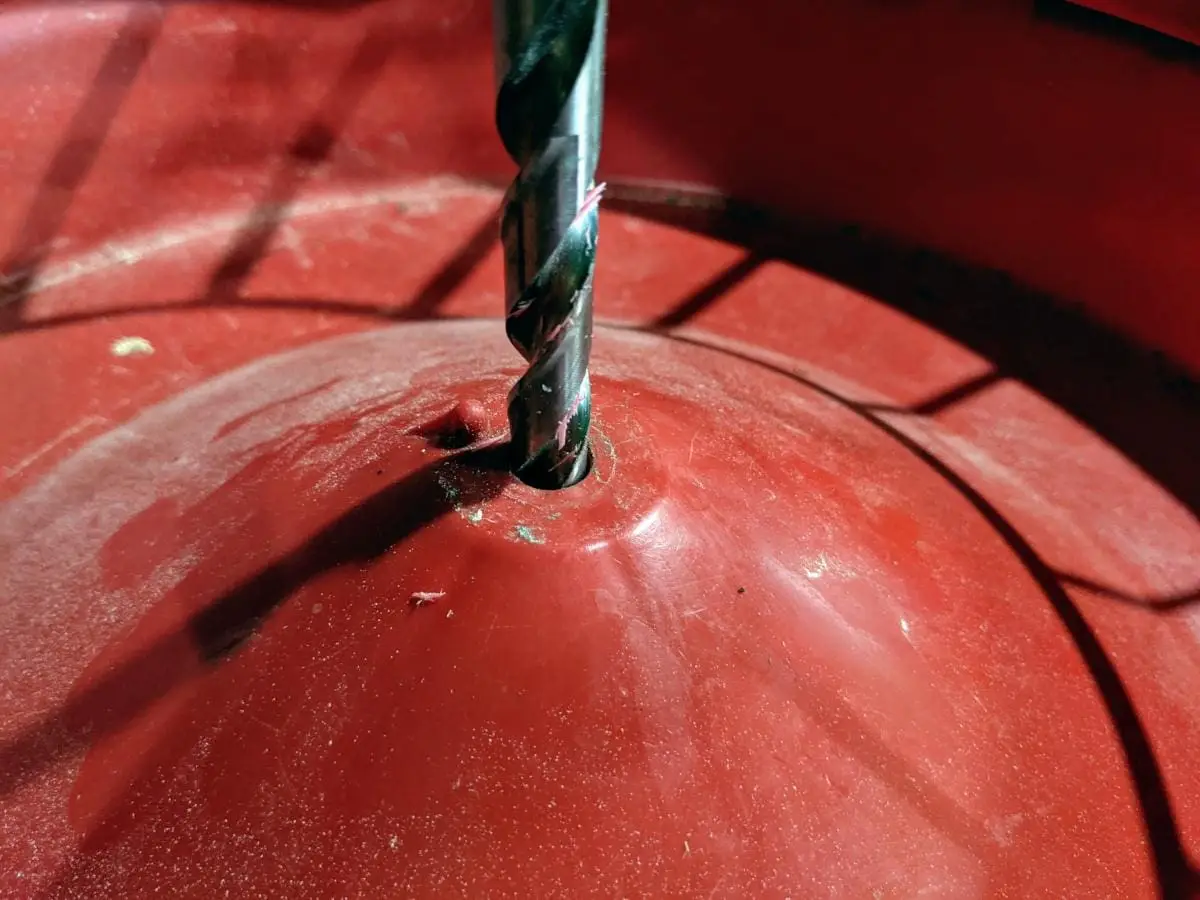
The only required modification to the rest of the feeder is that the base needs to be drilled out to receive a 1/2″ rod since the original aluminum shaft was 12 mm. The holes in the upper parts of the feeder are big enough to accomodate the threaded rod without any alterations. One bonus to note here is that the hopper height adjustment screw works better on the rough surface of the threaded rod than the smooth aluminum. We used to always find that the aluminum shaft allowed the hopper to creep downward over time.
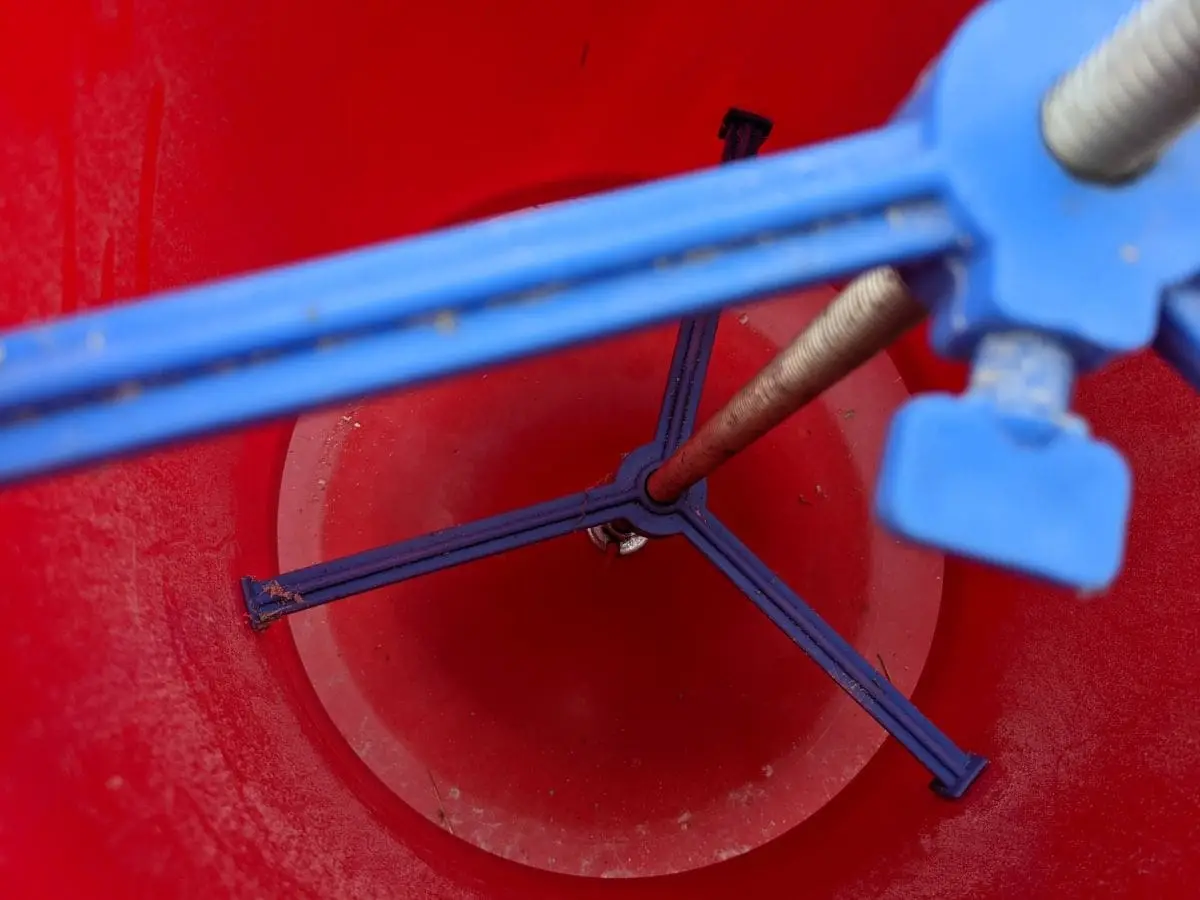
We’ve been using several of these repaired feeders this summer and so far, they’ve been working well. I hesitate to call anything a permanent fix, but I’m confident that these new steel shafts will do a better job and allow us to continue feeding pasture raised chickens for many more years.
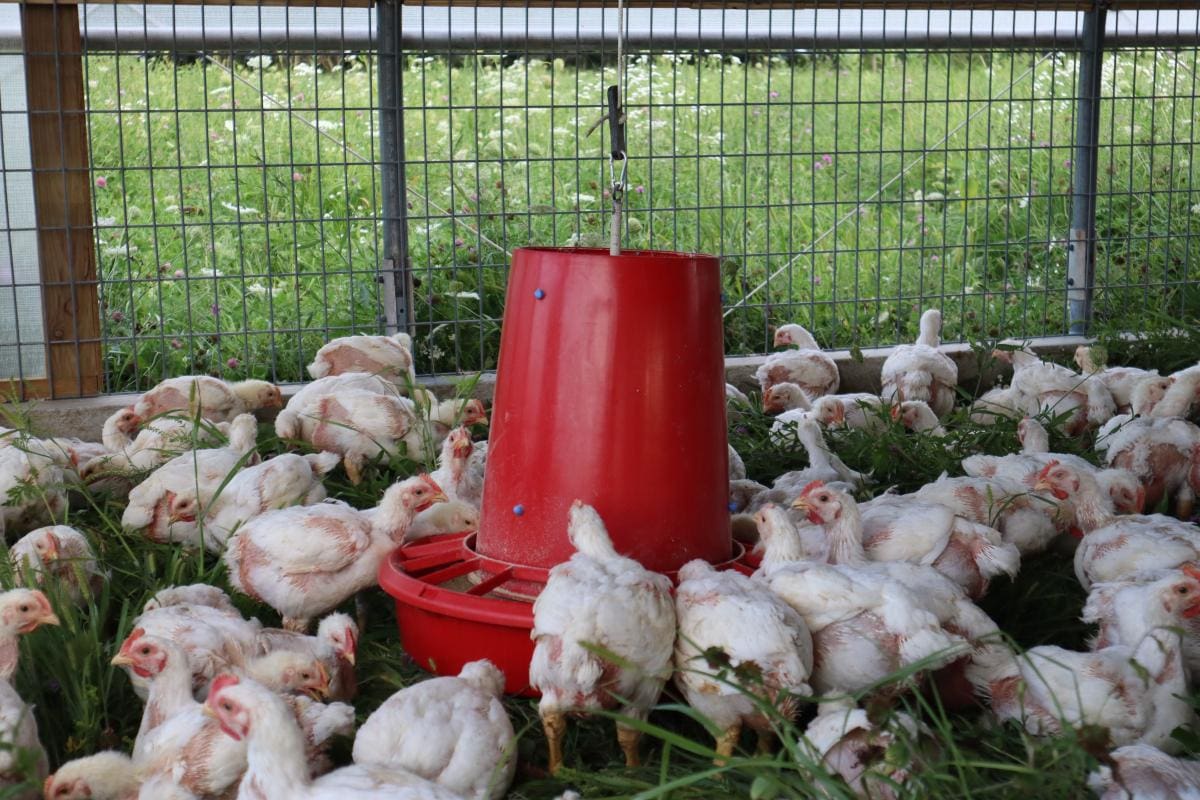